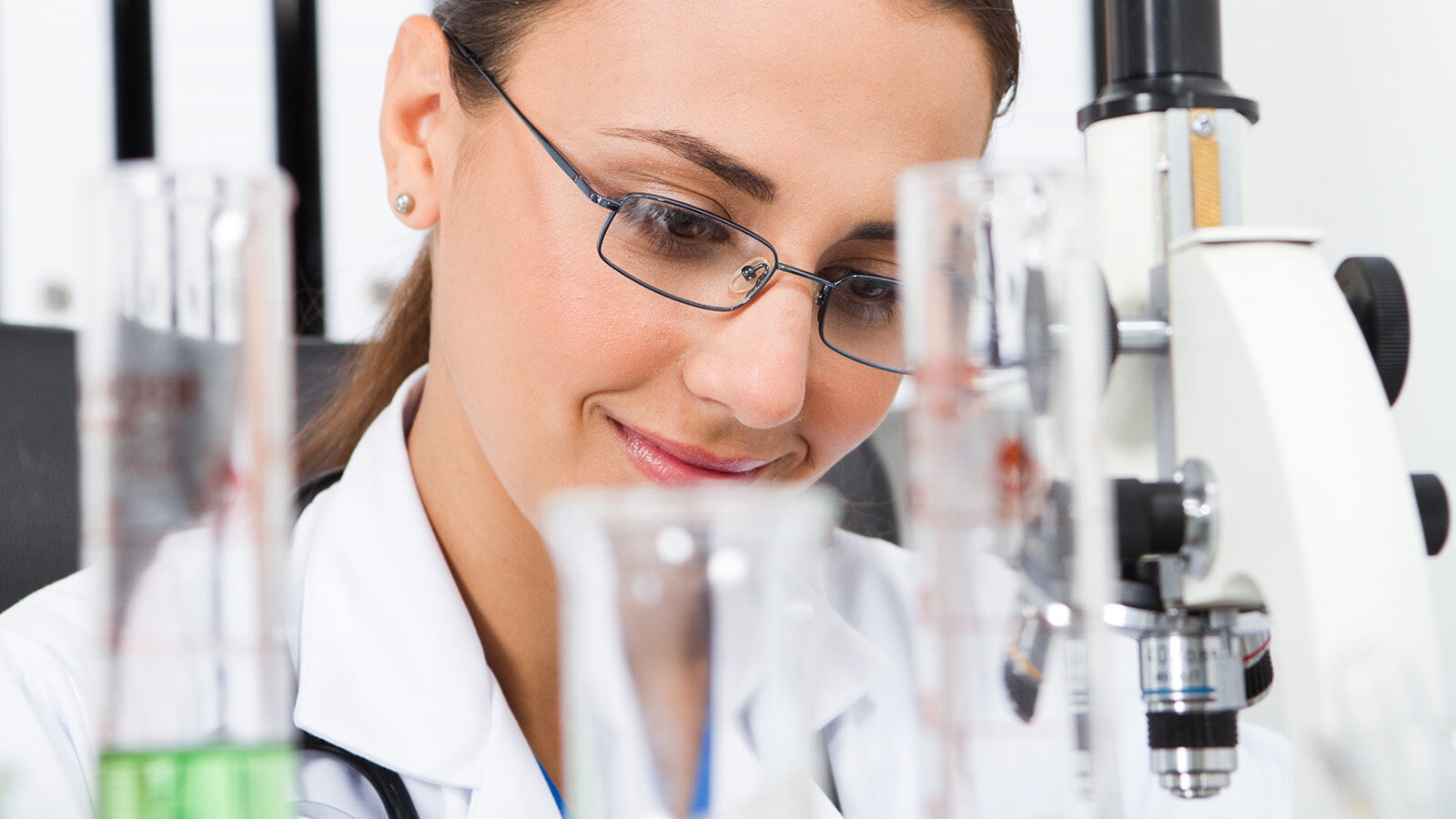
Extend the functionality of your LIMS
Additional Matrix Modules for our LIMS Solution
Additional LIMS Modules
Additional modules are available for our Matrix LIMS solutions which extend the functionality of our already highly configurable out-of-the-box laboratory information management systems.
Brief details are outlined below. To discuss individual project needs feel free to contact us so we can advise the best solutions for your company.
DISCOVER
Select your LIMS modules
- ICMS - Instrument Calibration & Maintenance System
- Competency Management Module
- Inventory Management Module
- Document Management Module
- Corrective and Preventive Action Management (CAPA) Module
- Scheduler
- SPC - Statistical Process Control
- iPlanner - Instrument Booking
- Bulk Sample Registration
- Frequency Testing
- Environmental Monitoring
- MIDAS - Matrix Instrument Data Acquisition System
- Laboratory Execution System (LES)
Matrix Instrument Calibration & Maintenance System (ICMS) Module
The Matrix ICMS module allows laboratories to easily track the calibration and maintenance history of every piece of equipment within the laboratory. This module can be linked into the work allocation part of Matrix Gemini to prevent the allocation of work to an un-calibrated instrument or one that has not been maintained correctly. ICMS uses the instrument table which stores information such as instrument manufacturer.

Competency Management Module
You can now match the competencies of users to the specific needs of their role within an organization. Ensure that users have their skills assessed and offer external regulators and management insight into skills gained to establish if further training is required.
Schedule training and re-training dates and track users confirmation from within the system. Block non-certified users from performing certain actions, such as entering results for specific test types. Certificates of competency can be distributed and stored for historical record of skills acquired. Automate the scheduling of outstanding training modules and refresher courses.

Inventory Manager Module
Matrix Inventory Manager provides integrated inventory management for laboratory materials including standards, reagents, raw materials and consumables. Key information about the inventory items are recorded including supplier, lot number, quantity, usage and expiry date.
A highly flexible module it manages all types of inventory with ease, managing the life cycle of the inventory from reception to disposal. All changes in status are logged. Inventory items can be assigned storage locations to aid tracking and help staff find the correct material quickly. Tests can require that specific inventory is allocated to ensure a fully traceable audit trail of items used in the laboratory.
Take control of the standards, consumables and reagents in your laboratory with the Matrix Inventory Manager.

Document Management Module
Track and manage all your key laboratory documents within the LIMS. Stores any sort of document format (PDF, Word, PNG, etc.). Manage the release, update and withdrawal of documents to appropriate staff. Version control provides a full audit trail and historical record for traceability.
Define and manage who can access them and record confirmation that staff have read, understood and agree to follow each version of every document. Trace document history of all documents, and all staff, and create reports for audit and other management purposes to prove that documents have been circulated and read by staff.

Corrective and Preventive Action Management (CAPA) Module
The CAPA Management Module is the perfect add-on to log issues or actions, and to ensure they are followed up and closed. You can call the CAPA module from virtually any screen and note issues as you want. It's perfect to note problems in the laboratory, actions that need resolution, or external customer feedback to feed into your quality improvement cycle.
Record all issues associated with quality and auditing within your organization. Issues/actions can be defined and allocated to staff, with outcomes stored within the system. Drive continual quality improvement across your whole organization by logging audit outcomes as well as customer comments and feedback. Reduce risk and the expense of continual root cause of issues; in turn improving staff and customer experiences, and financial performance. Modify CAPA screens and workflow to reflect the specific requirements of your organization. Report on specific areas of concern for your business.

Matrix Scheduler Module
Matrix Scheduler is an optional module for the Matrix Gemini LIMS product range. It allows tasks to be automatically scheduled based on dates, times, days of the week and other parameters. The Matrix Scheduler supports a full audit listing, allowing you to see and review all changes made to a schedule.
In addition, Matrix Scheduler provides a clear and easy method of adding additional tasks, without the need for an entirely new distribution of the product.
- Automatically schedule multiple jobs such as sample / batch registration thus saving personnel time
- Schedule reports to run automatically at any date and time, or at regular intervals, thereby enabling out of hours 24/7 operation. It can also adjust schedules automatically to avoid weekends and holidays. Work lists, summary reports and operational status of samples / tests can be ready for the working day
- Schedule triggering of external programs e.g. automate scheduled email reminders, reports, backups, any Microsoft program etc. so that they are ready for staff arriving at work or prior to important meetings or deadlines
- Matrix Scheduler provides a clear and easy method of adding tasks to the schedule and is delivered with easy to use and effective on-line documentation making the system user friendly and easy to support
- Matrix Scheduler automatically starts on server startup and is a server based standard Windows service background process that logs all work requests and their outcomes
- The current / future schedules can be viewed from anywhere on the network to verify / check logs that schedules have been run
- The system administrator has complete control over the schedule while allowing clients the benefit of scheduling times that are convenient for them

Matrix Statistical Process Control (SPC) Module
The Autoscribe Informatics Matrix Statistical Process Control (SPC) module allows the analysis of results using standard statistical techniques to detect data outliers and unusual trends. It is used extensively in manufacturing and quality control environments to give early warning of pending problems.

Matrix iPlanner (Instrument Booking) Module
An instrument booking system module is available for Matrix Gemini LIMS. The system allows for the automatic allocation of sample-tests to the appropriate instrument within constraints which include the booking of prerequisite tests, test order, sample availability dates and instrument capacities.
The benefits of employing this new module are more efficient use of expensive automated equipment and the ability to better balance the workload to meet testing deadlines The instrument plan can be viewed over desktop or browser clients.
Instrument bookings are displayed on a plan which is color coded to represent either an empty instrument, a partially loaded instrument, an instrument at capacity or an offline instrument. The view of the instrument plan can be expanded / compressed so that the user can view a wider or narrower range of dates.
Instruments are shown on the y-axis and time on the x-axis. At each interval where a booking is present the bar either displays the number of sample tests booked and the capacity (e.g. 4/10 showing 4 samples tests booked on an instrument with a capacity of 10) or “Offline” in the event of an instrument being offline for maintenance or calibration etc.
When an instrument booking is highlighted a list box gives details of the samples to be run on that instrument at that time point. Samples can be moved from one instrument booking to an alternative date using a point and click system.

Bulk Sample Registration Module
The Matrix Bulk Sample Registration Module provides huge time saving benefits for customers dealing with large numbers of samples or where there is a variety of sample types being registered.
A grid with spreadsheet-like data entry functionality for registering large numbers of samples is offered. The columns in the grid may be configured to suit specific customer requirements but typically they will include Sample Number (automatically or manually allocated), Submitter, Substance/Product and Tests (automatically or manually selected). A fill down feature allows fast data entry without the need to enter the same data multiple times. A fill down series is also available where specified numeric cells are incremented according to a specified pattern for each row in the grid. Other supporting data (e.g. target completion date) can be specified in columns before the registration takes place.
The completed grid can be used as a template if similar sets of samples are registered on a routine basis. Copy and paste functionality is supported, e.g. if sample details are in Excel format they can be directly copied into the Matrix grid.

Frequency Testing Module
The Matrix Frequency (or Selective) Testing Module allows the automatic allocation of reduced testing thus saving laboratory time. Parameters that may be specified include:
- Testing frequency for each test on a substance/product e.g. add test every nth sample registered
- Tests may be forced for the first 'n' samples of a new substance/product
- Full testing may be automatically allocated if a specified time period has elapsed since the last sample of a particular substance/product was tested
- Full testing may be automatically allocated following the failure of the current batch when test results are compared against limits

Environmental Monitoring Module
The Environmental Monitoring module simplifies and automates environmental monitoring in QA Labs. It allows graphical mapping of test results to sample point locations, enabling instant visualization of where problems are occurring. Test results at each sample point are shown as a graph and table, filtered by timescale, allowing easy analysis. Out of specification test results may be linked to corrective and preventive actions (CAPA) which may be easily logged within the LIMS. Test failures can trigger more frequent testing of that sample point according to preset criteria, enabling best practice environmental/hygiene monitoring even by non-specialist staff.
The Matrix Gemini Environmental Monitoring module is perfect for a wide variety of industries including Food and Beverage, Pharmaceutical, Medical Devices, Cosmetics and Healthcare - anywhere where regular testing with swabs, settle plates or air filtration monitoring is used to determine the level of microbial contamination to ensure hygienic/sterile conditions.

Matrix Instrument Data Acquisition System Module
Autoscribe’s Matrix Instrument Data Acquisition System (MIDAS) module allows you to connect a wide variety of laboratory instruments and equipment to Matrix Gemini LIMS. MIDAS provides a flexible and repeatable way to capture and record data accurately and quickly, with the added advantage of helping to ensure the integrity of the information.
Once setup MIDAS will run automatically in the background providing an invisible link between laboratory instruments and the LIMS. This avoids tediously transcribing data by hand or manually manipulating data in spreadsheets, both of which are error prone. MIDAS provides a defendable, robust and effective methodology to ensure compliance with standards such as ISO17025 and GMP. Capturing test results into the LIMS also makes your laboratory more efficient, dramatically reducing costs and enabling higher levels of automation.

Laboratory Execution System (LES)
Encourage a structured working environment in your laboratory. Ensure standard operating procedures are followed and tasks are completed in a controlled and repeatable way.
The Matrix Laboratory Execution System (LES) defines the workflow, or steps associated with a laboratory method or process, to ensure that Standard Operating Procedures (SOPs) or best practices are always followed. Define unlimited workflows, each with an unlimited number of steps, and each step consists of one or more actions. The Matrix LES provides structure to busy laboratories to ensure that tasks are never missed, sample results and meta data are recorded as required, and a complete audit trail of all key steps and actions is kept.

Let’s Talk
Ready to get started? Contact us today.
Let’s connect and we’ll arrange a Matrix LIMS demo.